Working Of Ball Milling For Making Nanoparticles
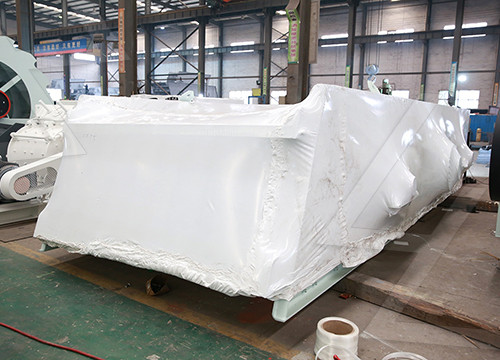
Ball milling: a green technology for the preparation
The ball mill Ball milling is a mechanical technique widely used to grind powders into ne particles and blend materials.18 Being an environmentally-friendly, cost-effective
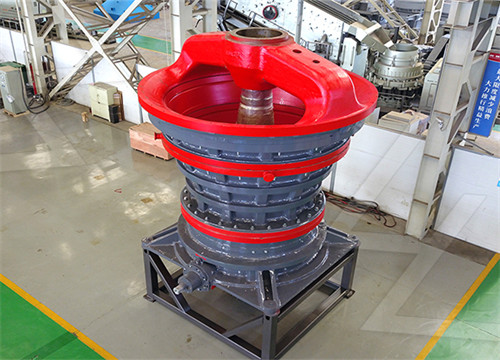
High-Energy Ball Milling an overview ScienceDirect
2.1.1 High energy ball milling (HEBM) The HEBM method may often involve working at high temperature and pressure. There may be possibility that the temperature may reach
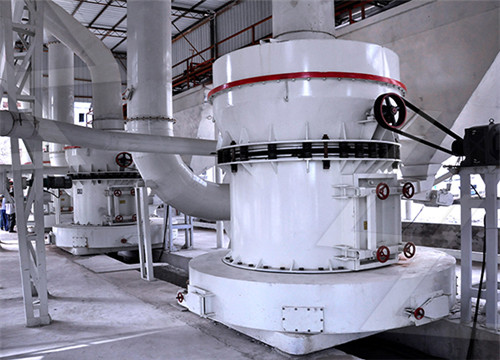
进一步探索
(PDF) High Energy Ball Mill ProcessingHigh-Energy Ball Milling 1st Edition根据热度为您推荐•反馈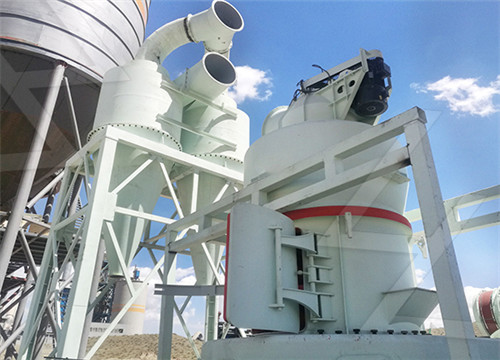
Ball Milling method for synthesis of nanomaterials
This powder will be made into nanosize using the ball milling technique. A magnet is placed outside the container to provide the pulling force to the material and this magnetic force
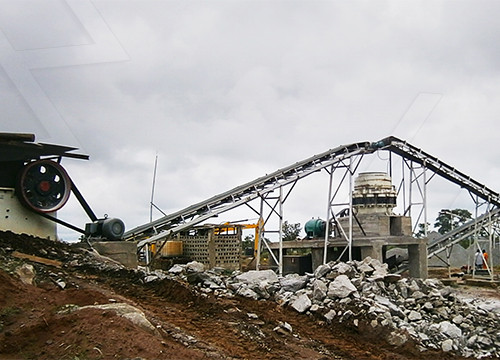
High energy ball milling process for nanomaterial synthesis
During the high-energy ball milling process, the powder particles are subjected to high energetic impact. Microstructurally, the mechanical alloying process can be divided into four stages: (a) initial stage, (b)
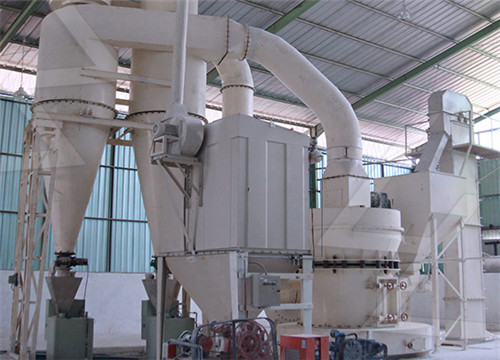
Ball milling synthesis of silica nanoparticle from limestone husk
The results have revealed that the nano-sized amorphous silica particles are formed after about 6 h ball milling and they are spherical in shape. The average particle size of the
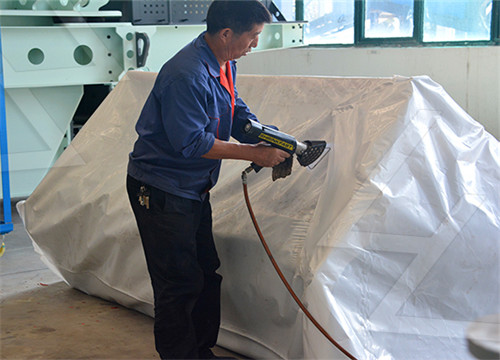
Ball Milling an overview ScienceDirect Topics
Ball milling, a shear-force dominant process where the particle size goes on reducing by impact and attrition mainly consists of metallic balls (generally Zirconia (ZrO2) or steel
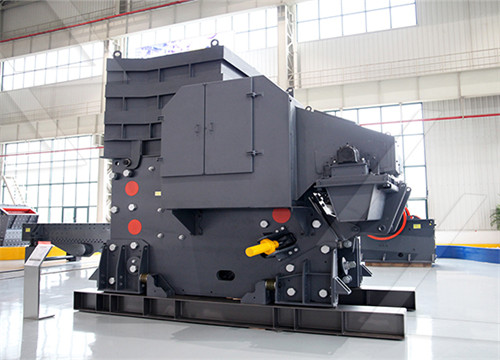
Grinding Down to the Nanoscale with Planetary Ball Mills
2013年4月3日The mill derives its name from the unique kinematics wherein the grinding bowls are mounted on a rotating "sun" disk that rotate in the opposite direction around the disk centre. Because of this, the
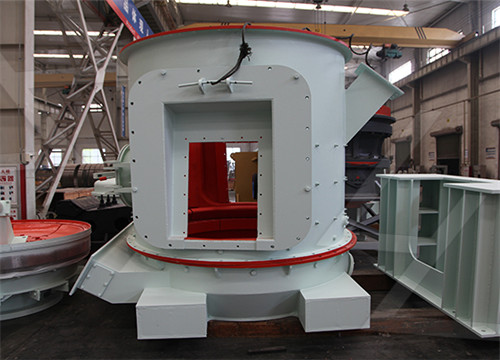
Ball milling machine for nanoparticles fabrication NEWS
Ball milling for nanoparticle fabrication. Ball milling is a particulate matter processing technique that can be used to produce nanoparticles from a variety of materials. The
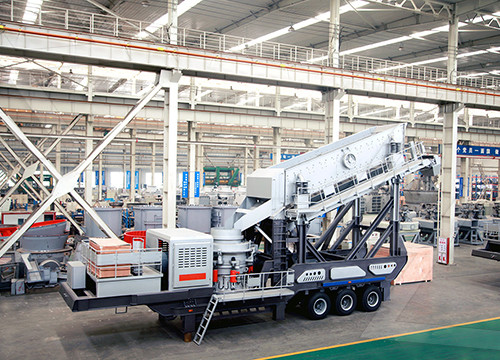
Nano Grinding MillsMethods — When Smallest is Best
Jet milling with superheated steam enables nano-range particle sizes while also drying the feed material. Steam can be introduced into the grinding chamber at higher pressure
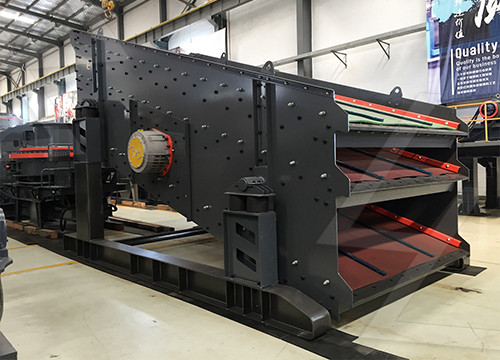
Ball milling: a green technology for the preparation and
Ball milling in aqueous conditions was also employed by the Wang group to obtain cellulose nanofibers from pulp. 49 In particular, they first treated dried the soft pulp in water at room temperature to loosen the hydrogen bonding between the fibres, then they milled the resulting loosened fibres in aqueous medium for 2 hours.
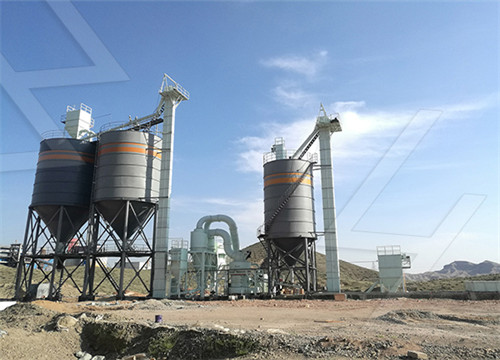
Ball milling: a green technology for the preparation and
The ball mill Ball milling is a mechanical technique widely used to grind powders into ne particles and blend materials.18 Being an environmentally-friendly, cost-effective technique, it has found wide application in industry all over the world. Since this mini-review mainly focuses on the conditions applied for the prep-
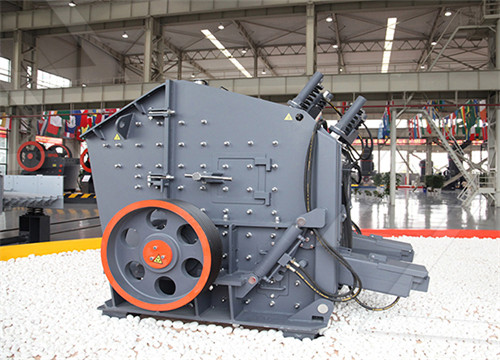
Fabrication and evaluation of gold nanoparticles by ball milling, Hall
2021年1月1日The aim of this stone is to use a high-energy ball mill to convert micro-sized Au powder into nano-structured Au powder; it means Au (Gold) NanoParticles (AuNPs) have been fabricated in this present work. The ball
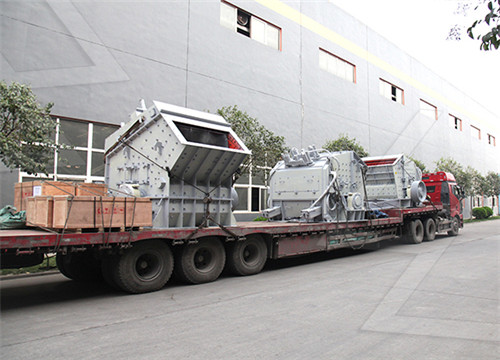
High energy ball milling process for nanomaterial
The impact energy of the milling balls in the normal direction attains a value of up to 40 times higher than that due to gravitational acceleration. Hence, the planetary ball mill can be used for high-speed milling.
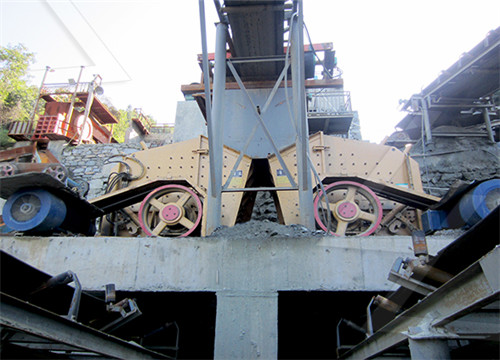
A promising mechanical ball-milling method to synthesize
2017年9月5日More importantly, the ball-milling treatment also promotes the carbon layer and Co 9 S 8 combining with each other more effectively to form an ultrafine nanocomposite which favors the electrons transporting and accommodates the volume expansion/contraction during the charge–discharge process. Synthesis of Co 9 S 8 /C
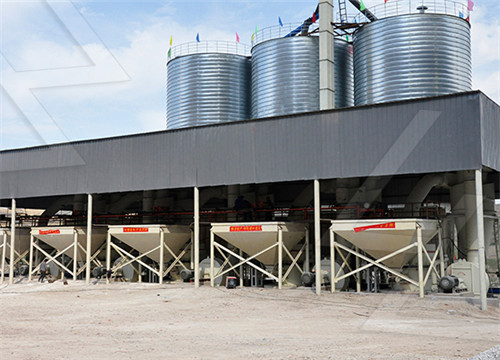
Ball milling synthesis of silica nanoparticle from limestone husk ash
The results have revealed that the nano-sized amorphous silica particles are formed after about 6 h ball milling and they are spherical in shape. The average particle size of the silica powders is found to be around 70 nm which decreases with increasing ball milling time or mill rotational speed.
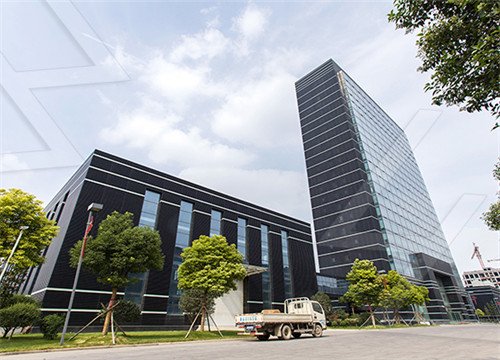
Grinding Down to the Nanoscale with Planetary Ball
2013年4月3日The mill derives its name from the unique kinematics wherein the grinding bowls are mounted on a rotating "sun" disk that rotate in the opposite direction around the disk centre. Because of this, the
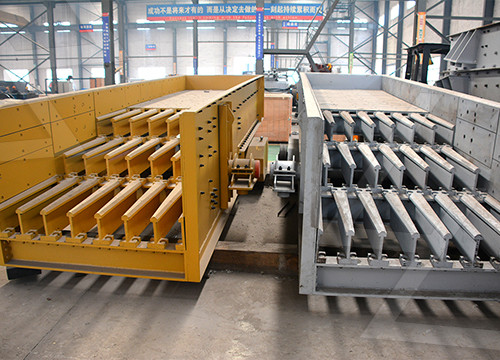
Preparation of Nd–Fe–B nanoparticles by surfactant-assisted ball
2009年2月12日The SmCox (x=3.5, 4, 5, 6, 8.5, and 10) magnetic nanoparticles with different composition have been prepared by surfactant-assisted ball milling technique.
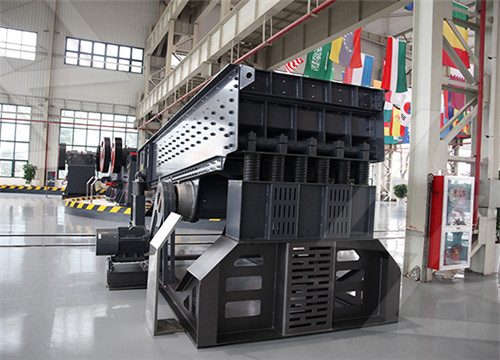
Influence of ball milling on the particle size and antimicrobial
Influence of ball milling on the particle size and antimicrobial properties of Tridax procumbens leaf nanoparticles doi: 10.1049/iet-nbt.2016.0028. Authors Subramani Karthik 1,Rangaraj Suriyaprabha 1,Kolathupalayam Shanmugam Balu 1,Palanisamy Manivasakan 1,Venkatachalam Rajendran 2 Affiliations
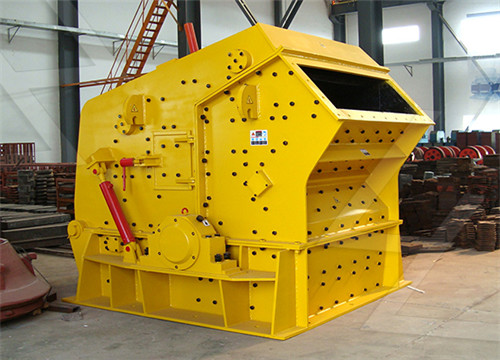
Catalysts Free Full-Text Ball Milling-Assisted Synthesis of
2019年3月5日As shown in Scheme 1, we successfully fabricated Ru 2 P nanoparticles embedded in carbon (Ru 2 P-BM-C) via a simple solid-state ball milling-assisted technique . To be specific, a mixture of ruthenium chloride, sodium hypophosphite, and commercial carbon black (VXC-72R, Cabot) were first milled in a planetary ball mill for 2 h.
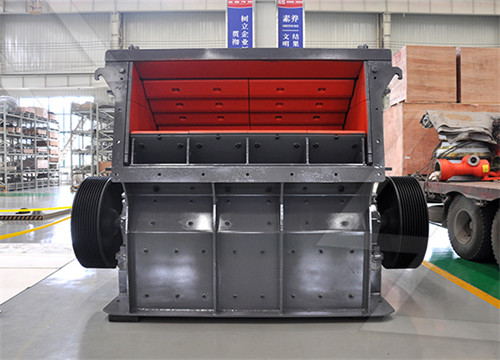
Ball Mill an overview ScienceDirect Topics
Quantum Nanostructures (QDs): An Overview. D. Sumanth Kumar, H.M. Mahesh, in Synthesis of Inorganic Nanomaterials, 2018 3.6.1.1 Ball Milling. A ball mill is a type of grinder used to grind and blend bulk material into QDs/nanosize using different sized balls. The working principle is simple; impact and attrition size reduction take place as the ball
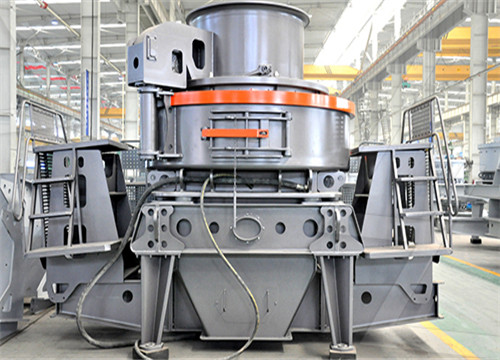
Ball‐milling treatment of Nb and B nanoparticles modified
2023年2月22日Ball milling treatment is a low-cost and achievable large-scale production method for preparing the composite powder used for the laser powder bed fusion (LPBF) process. For the ball-milled composite powder, good powder spreadability and composition homogeneity are essential for obtaining the LPBF-fabricated part with good forming quality.
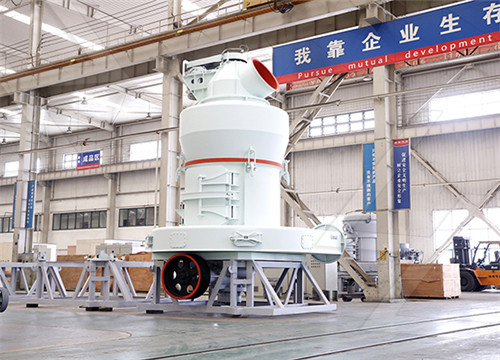
Nano Ball‐Milling Using Titania Nanoparticles to Anchor Cesium
2020年9月2日In this work, a room temperature mechanochemical method is presented to construct TiO 2 @CsPbBr 3 hybrid architectures, in which TiO 2 nanoparticles (NPs) with a hard lattice as nano “balls” mill off the angles and anchor to the CsPbBr 3
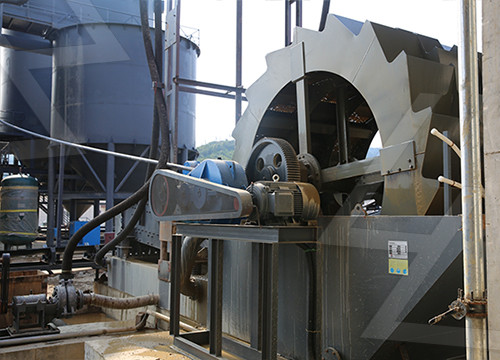
Synthesis of iron-doped TiO2 nanoparticles by ball-milling
2014年7月22日In this research work, TiO 2 nanoparticles were doped with iron powder in a planetary ball-milling system using stainless steel balls. The correlation between milling rotation speeds with structural and morphologic characteristics, optical and magnetic properties, and photocatalytic abilities of bare and Fe-doped TiO 2 powders was studied
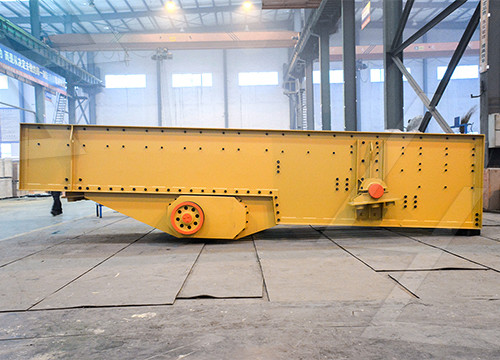
Ball milling: a green technology for the preparation and
Ball milling in aqueous conditions was also employed by the Wang group to obtain cellulose nanofibers from pulp. 49 In particular, they first treated dried the soft pulp in water at room temperature to loosen the hydrogen bonding between the fibres, then they milled the resulting loosened fibres in aqueous medium for 2 hours.
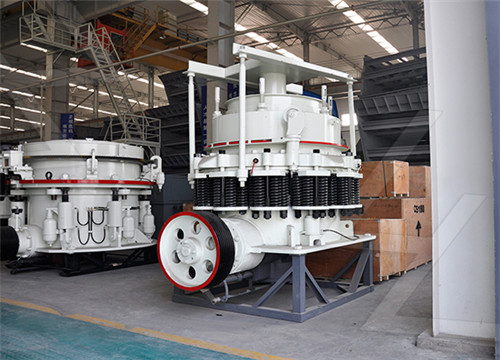
Aluminum nanoparticles manufactured using a ball
Well-formed aluminum nanoparticles with average particle sizes of approximately 30 nm and high specific surface areas of over 30 m 2 g −1 can be obtained using the optimal ball-milling reaction time. In this
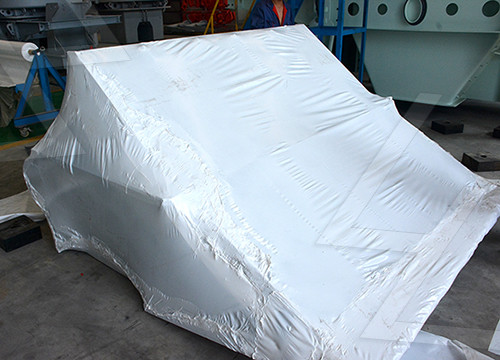
Fabrication and evaluation of gold nanoparticles by ball milling, Hall
2021年1月1日The aim of this stone is to use a high-energy ball mill to convert micro-sized Au powder into nano-structured Au powder; it means Au (Gold) NanoParticles (AuNPs) have been fabricated in this present work. The ball
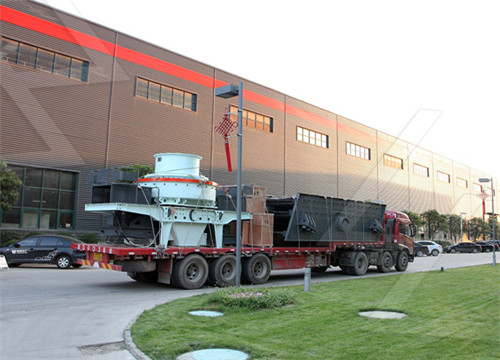
High energy ball milling process for nanomaterial
The impact energy of the milling balls in the normal direction attains a value of up to 40 times higher than that due to gravitational acceleration. Hence, the planetary ball mill can be used for high-speed milling.
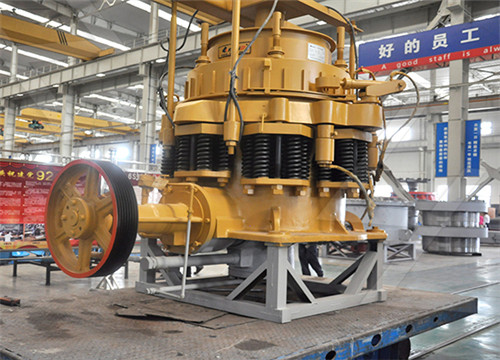
Ball milling synthesis of silica nanoparticle from limestone husk ash
The results have revealed that the nano-sized amorphous silica particles are formed after about 6 h ball milling and they are spherical in shape. The average particle size of the silica powders is found to be around 70 nm which decreases with increasing ball milling time or mill rotational speed.
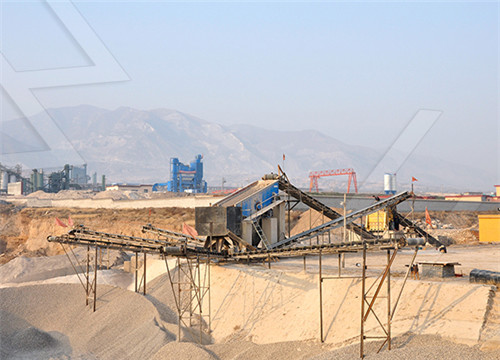
Grinding Down to the Nanoscale with Planetary Ball
2013年4月3日The mill derives its name from the unique kinematics wherein the grinding bowls are mounted on a rotating "sun" disk that rotate in the opposite direction around the disk centre. Because of this, the
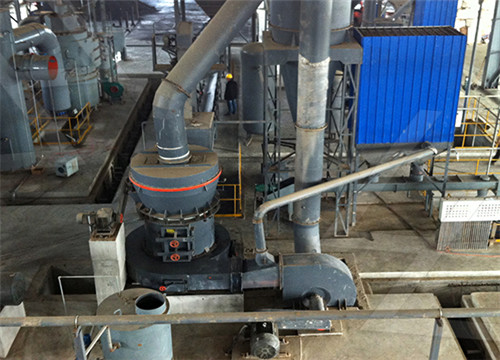
Influence of ball milling on the particle size and antimicrobial
Influence of ball milling on the particle size and antimicrobial properties of Tridax procumbens leaf nanoparticles doi: 10.1049/iet-nbt.2016.0028. Authors Subramani Karthik 1,Rangaraj Suriyaprabha 1,Kolathupalayam Shanmugam Balu 1,Palanisamy Manivasakan 1,Venkatachalam Rajendran 2 Affiliations
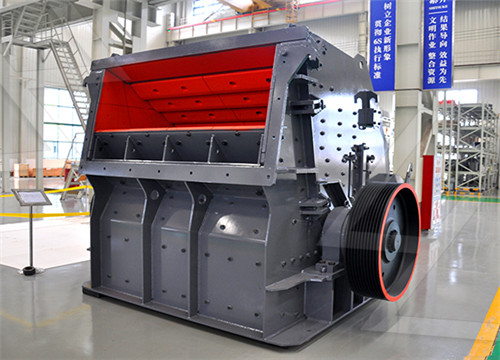
Preparation of Nd–Fe–B nanoparticles by surfactant-assisted ball
2009年2月12日The SmCox (x=3.5, 4, 5, 6, 8.5, and 10) magnetic nanoparticles with different composition have been prepared by surfactant-assisted ball milling technique.
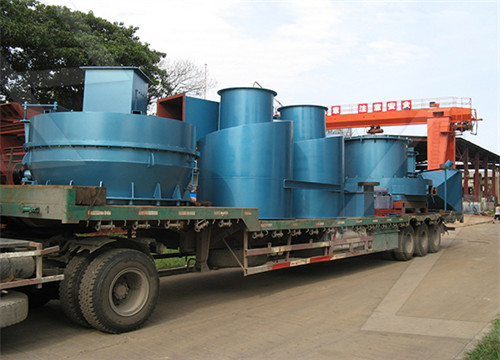
Catalysts Free Full-Text Ball Milling-Assisted Synthesis of
2019年3月5日As shown in Scheme 1, we successfully fabricated Ru 2 P nanoparticles embedded in carbon (Ru 2 P-BM-C) via a simple solid-state ball milling-assisted technique . To be specific, a mixture of ruthenium chloride, sodium hypophosphite, and commercial carbon black (VXC-72R, Cabot) were first milled in a planetary ball mill for 2 h.
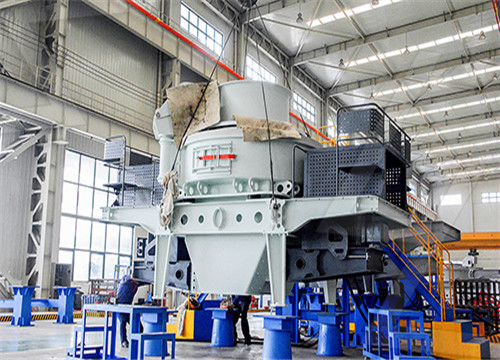
EFFECT OF MILLING TIME ON PRODUCTION OF ALUMINIUM NANOPARTICLE BY
High-energy ball milling is a promising and effective technique for the production of aluminium nanoparticles. Elemental aluminium powder of 325 mesh, 99.5% purity is taken for this investigation. A planetary ball mill, PM 100, with tungsten carbide balls of diameter 9.5 mm was used. The vial containing 62 g of powder and 620 g of tungsten carbide
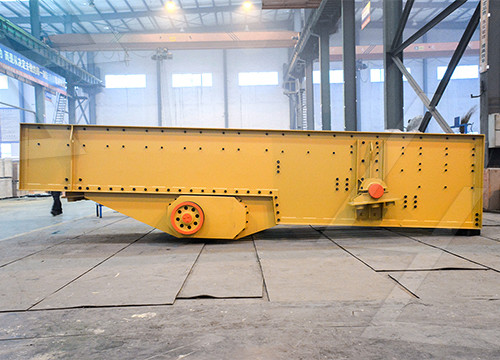
Nano Ball‐Milling Using Titania Nanoparticles to
2020年9月2日In this work, a room temperature mechanochemical method is presented to construct TiO 2 @CsPbBr 3 hybrid architectures, in which TiO 2 nanoparticles (NPs) with a hard lattice as nano “balls” mill off the
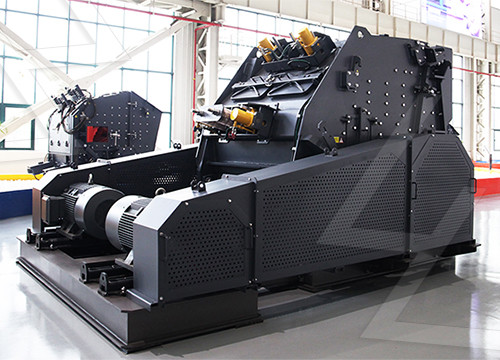
Mechanical Milling: a Top Down Approach for the Synthesis of
2012年2月3日The ball-milling contributed to a decrease in the particle size of SWCNTs and Si particles and to an increase in the electrical contact between SWCNTs and Si particles in the SWCNT/Si composites. 3.8. Some Other Nanomaterials and Nano Composites Lee et al[104] studied the Phase evolution of Fe 2 O 3 nanoparticle during
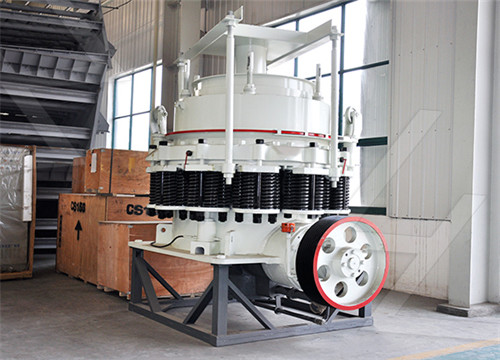
Synthesis of iron-doped TiO2 nanoparticles by ball-milling
2014年7月22日In this , we report that ball milling can be used as a powerful low-cost and “green” method to produce Fe-doped TiO 2 nanoparticles, which can be applied as an efficient photocatalyst for large-scale photocatalytic oxidation of dye pollutants present in the effluents of textile industries.
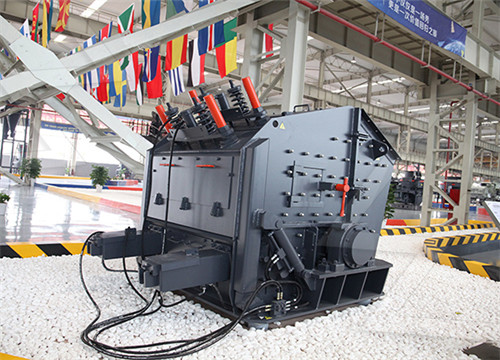
Synthesis of magnetite nanoparticles from iron sand by ball-milling
2019年4月1日The research aims to synthesis of magnetite nanoparticle from iron sand by mechanomhemical route. The XRF graph of showed the dominant mineral content of the iron sand is SiO 2 (36.09%), Fe 2 O 3 (34.015%) and Al 2 O 3 (10.034%). Hereinafter, the Iron oxide nanoparticle synthesized by the ball mill method at different milling time.
- 碎石场安全生产
- 振动筛的供应商
- 瑞典进口破碎设备那里买
- 山西省太原煤校
- 中型打沙机多少钱一台
- Rock Stone By Rock Stone Crusher Machine
- 欧版颚破11001200有什么特点
- 石英砂厂用什么设备
- GP500圆锥破碎机说明书
- 喷塑加工设备
- Accounting For Quarry Crusher Business Welcome To Accounting For Manag
- Minas De Cobre Da Tanzania Para Businesss
- 600X900鄂式破碎机价格
- Aluminum Can Recycling Equipment
- Stone Crusher Supplier In